Reaching new heights
Centennial College is a leader in avionics, aircraft maintenance and aerospace manufacturning education. Located in the North York region of the Greater Toronto Area, its Downsview Campus is now home to the Bombardier Centre for Aerospace and Aviation; a revolutionary facility that houses the college’s long-running aerospace and aviation programs.
The four-acre, 138,000 sq. ft. Bombardier Centre features two aircraft hangars, custom-purpose-built labs and electro-mechanical systems, as well as new classrooms and faculty office spaces. Centennial repurposed the historic De Havilland building located in Downsview Park in Toronto to house its aircrafts and equipment, and to create a space to teach aviation students how to save lives by repairing and maintaining aviation systems. At the time of its opening, Centennial was one of the largest campuses dedicated to aerospace and aviation education in North America. Additionally, the development enabled the college to offer new aerospace manufacturing programs.
Designed by award-winning architecture firm Maclennan Jaunkalns Miller Architects, the Bombardier Centre blends history with contemporary construction. Fully equipped with state-of-the-art equipment and technology, the Bombardier Centre offers students a space to explore the evolution of aviation technology, while encouraging connections with academic and industry partners.
A collaborative approach
Blending modern construction with an existing historic site was a complex undertaking that required specialized expertise beyond the college’s existing resources. The De Havilland building sits on federally owned land, requiring the project team to liaise and collaborate with various levels of government to preserve history amidst necessary renovations.
Centennial College brought in our team to supplement its capacity and support its objective to open the facility to students and faculty by Winter 2019. Our team provided comprehensive project management, furniture, equipment planning, procurement support and move management services. To help achieve the college’s deadline, we prioritized the project requirements and worked in collaboration with Centennial’s in-house team to monitor and mitigate risks.
“The construction of the Downsview Campus is a story of incredible coordination and trust. The stakes were high with absolutely no room for error. Despite the risks, Colliers Project Leaders worked with me every step of the way to deliver the new campus.”
Former Associate Vice President, Corporate Services, Centennial College
Managing risks
Throughout construction, our team proactively identified risks and challenges that might impact delivery. When the general contractor became insolvent in the midst of construction, the college required a different approach to complete the project in time for the winter semester.
Our team quickly outlined the options that the college had available and put forward a recommendation. Focused on its students and providing this new space, the college directed us to get “bums in seats” on time, as promised. With this as our guiding principle, we began to implement new measures to keep the trades paid and working while also working with the contractor’s team to keep the project moving forward. This realignment proved to be invaluable, although it did take time to work through the details and keep each team fully engaged.
As the project team developed a backup plan to manage the insolvent general contractor, scheduled equipment deliveries began to arrive. With construction falling behind schedule, our furniture and equipment planning teams acted quickly to avoid a major equipment backlog or additional handling and storage fees. We negotiated with equipment vendors to defer or hold deliveries, while the college secured a vacant aircraft hanger nearby to use as storage. Once available, our team prepared the hanger with shelving, storage cages and security. We diverted the remaining equipment orders to the hanger for storage until the new facility was complete.
Major equipment – including modern and antique planes – also had to be relocated from the former site in Scarborough to the new location near the Downsview airport. To accommodate these sensitive and important assets, we arranged to have a new concrete pad poured less than a week before the planes arrived on the runway. This was a key task as the concrete pad required seven days to cure. The project team just met this timeline, which allowed the planes to have access to the hangar.
To facilitate the overall effort of the project, our furniture, equipment and move readiness project manager created a colour-coded dashboard to coordinate site access with construction progress, and manage equipment and supply deliveries. This became a pivotal tool to support and advance the project timeline. With equipment and supply deliveries handled, the trades were able to redirect their focus to complete construction on time and on budget.
“Colliers Project Leaders joined Centennial College initially to provide project management as an owner’s representative, and over the course of the project became valuable partners working alongside college leadership, advising and supporting the project in every way.”
Former Associate Vice President, Corporate Services, Centennial College
Establishing trust
Establishing trust with the wider project team was a critical part of the successful project delivery. Our team provided constant, clear communication to help maintain the critical schedule components that allow operational readiness activities to fall into place. Our entire support team focused on building strong relationships with the trades through regular check-ins, meetings and on-site follow-ups. Committed to completing the project on time, we deployed additional resources to monitor the progress of the project, and mitigate and manage risks daily.
Paving a new path
By assessing the risks and implementing creative solutions, the Bombardier Centre for Aerospace and Aviation opened in time for the 2019 winter semester. Equipped with the latest in aviation tools and technology, the modern, high-tech facility is a juxtaposition of the old and the new; the past and the future. Jets and helicopters sit adjacent to classrooms, ready for future aviation experts to explore as they learn and grow.
Images courtesy of Scott Norsworthy
Higher Education Brochure
View Now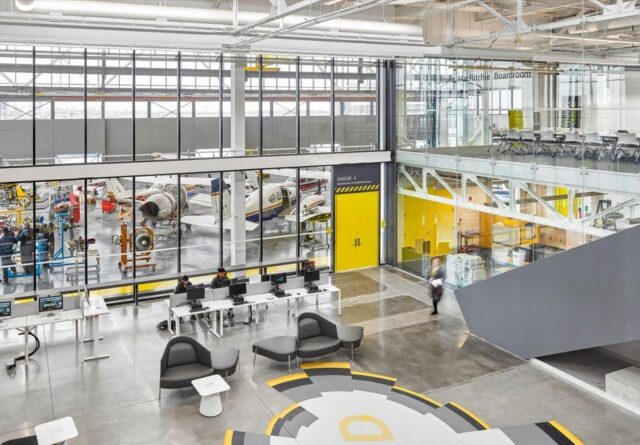
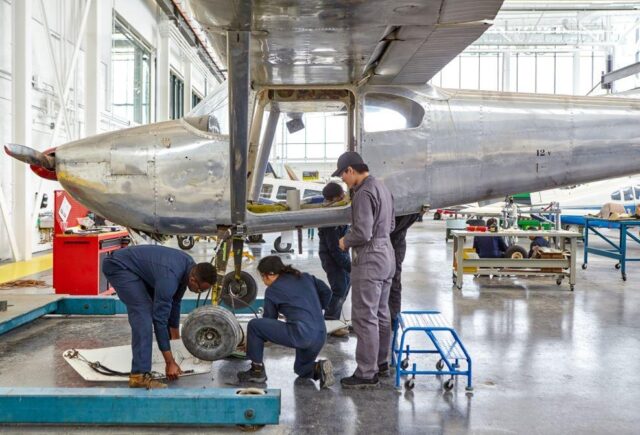